Understanding Porosity in Welding: Exploring Reasons, Impacts, and Prevention Methods
Porosity in welding is a persistent challenge that can significantly impact the quality and integrity of welds. As professionals in the welding industry are aware, recognizing the causes, results, and prevention strategies connected to porosity is critical for accomplishing durable and trusted welds. By diving into the origin of porosity, examining its detrimental effects on weld quality, and discovering effective prevention strategies, welders can boost their expertise and abilities to create high-grade welds consistently. The detailed interaction of elements adding to porosity requires an extensive understanding and a positive strategy to make certain successful welding end results.
Common Sources Of Porosity
Porosity in welding is mostly brought on by a mix of variables such as contamination, incorrect shielding, and poor gas protection throughout the welding procedure. Contamination, in the form of dust, grease, or rust on the welding surface area, develops gas pockets when heated, causing porosity in the weld. Inappropriate shielding takes place when the shielding gas, commonly utilized in processes like MIG and TIG welding, is incapable to fully shield the liquified weld pool from reacting with the surrounding air, causing gas entrapment and succeeding porosity. Furthermore, insufficient gas protection, typically due to wrong flow prices or nozzle positioning, can leave parts of the weld unprotected, permitting porosity to create. These aspects jointly add to the development of voids within the weld, weakening its honesty and potentially creating structural problems. Comprehending and addressing these typical reasons are critical action in stopping porosity and making sure the top quality and toughness of bonded joints.
Results on Weld Top Quality
The existence of porosity in a weld can dramatically endanger the general high quality and honesty of the welded joint. Porosity within a weld creates spaces or tooth cavities that damage the structure, making it more susceptible to fracturing, corrosion, and mechanical failure. These gaps serve as tension concentrators, decreasing the load-bearing capacity of the weld and boosting the likelihood of premature failing under applied tension. Additionally, porosity can additionally work as prospective websites for hydrogen entrapment, more intensifying the destruction of the weld's mechanical buildings.
Additionally, porosity can prevent the efficiency of non-destructive testing (NDT) strategies, making it challenging to identify various other issues or suspensions within the weld. This can cause substantial safety issues, particularly in important applications where the structural honesty of the bonded parts is paramount.
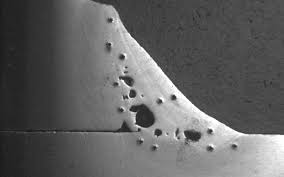
Avoidance Techniques Introduction
Given the damaging impact of porosity on weld top quality, reliable avoidance strategies are critical to preserving the architectural integrity of welded joints. One of the main avoidance methods is thorough cleansing of the base products prior to welding. Impurities such as oil, oil, rust, and dampness can add to porosity, so guaranteeing a tidy work surface area is necessary. Correct storage space of welding consumables in completely dry problems is also critical to avoid dampness absorption, which can bring about gas entrapment during welding. In addition, picking the appropriate welding criteria, such as voltage, present, and take a trip speed, can aid minimize the threat of porosity formation. Guaranteeing adequate securing gas circulation and coverage is one more essential prevention strategy, as inadequate gas insurance coverage can cause atmospheric contamination and porosity. Ultimately, appropriate welder training and qualification are essential for applying preventative procedures properly and regularly. By integrating these prevention methods into welding practices, the occurrence of porosity can be dramatically decreased, causing stronger and extra reputable bonded joints.
Value of Proper Shielding
Proper protecting in welding plays important site an important function in stopping climatic contamination and ensuring the stability of welded joints. Shielding gases, such as argon, helium, or a mix of both, are typically utilized to secure the weld swimming pool from reacting with elements in the air like oxygen and nitrogen. When these responsive elements come right into call with the hot weld swimming pool, they can trigger porosity, causing weak welds with reduced mechanical buildings.

Insufficient protecting can cause different flaws like porosity, spatter, and oxidation, endangering the structural honesty of the welded joint. Sticking to proper securing practices is essential to generate premium welds with marginal problems and make certain the durability and reliability of the welded parts.
Monitoring and Control Techniques
How can welders efficiently keep an eye on and regulate the welding process to ensure optimal outcomes and protect against defects like porosity? One trick approach is through using advanced surveillance technologies. These can consist of real-time monitoring systems that supply feedback on specifications such as voltage, present, travel speed, and gas circulation prices. By continuously keeping track of these variables, welders can determine inconsistencies from the excellent conditions and make prompt modifications to avoid porosity development.

Furthermore, applying appropriate training programs for welders is necessary for keeping an eye on and controlling the welding process successfully. What is Porosity. Enlightening welders on the value of keeping constant criteria, such as proper gas shielding and hop over to these guys take a trip rate, can aid avoid porosity issues. Normal evaluations and certifications can likewise guarantee that welders excel in monitoring and controlling welding procedures
Moreover, the use of automated welding systems can improve tracking and control capabilities. These systems can precisely control welding specifications, decreasing the probability of human error and guaranteeing regular weld high quality. By incorporating innovative monitoring modern technologies, training programs, and automated systems, welders can efficiently monitor and regulate the welding process to lessen porosity issues and attain top notch welds.
Verdict
